It was time for something big. In 2005, Everland had virtually nothing new since the International Monetary Fund (IMF) foreign exchange crisis in November 1997. The last ones were the water park ‘Caribbean Bay’ that opened in 1996 and the attraction ‘Columbus Adventure’ that was introduced in early 1998.
The master plan was roughly this: ‘Let’s bring in a large-scale roller coaster with enough capacity to minimize customer waiting time.’ The marketing department preferred a state-of-the-art roller coaster that Korea didn’t have. There was a strong desire to show customers something that would make them say, “Wow!”
Planning Team Manager Kim Hwan-tae (then 33 years old, currently an executive director at Jeju Shinhwa World) had a different idea. ‘Isn’t there something that blends well with nature, has a grand scale, is fun to ride for a long time, and is also incredibly enjoyable after the ride?’
● What is the fun of amusement rides?
The planning team conducted a large-scale customer survey. The core question was, “What do you think makes amusement rides fun?” The most common answer was “thrill.” If this were to continue, a thrilling, heart-pounding, 4th generation roller coaster would be the right choice. Manager Kim tilted his head. Are thrills and fun proportional?
I read the questionnaire from beginning to end, page by page. There was one passage that really caught my eye.
“Among those who answered ‘thrills are fun,’ there were those who answered ‘the only ride I can ride is the carousel.’” Eureka!
‘Thrill is fun’ can be interpreted not as ‘the greater the thrill, the more fun’, but as ‘if you provide a level of thrill that customers can handle, that’s fun’. For someone whose tolerable thrill intensity is 5, a 10-level ride is just a pie in the sky. ‘Full of thrills’ doesn’t necessarily guarantee 100% fun and success. If you provide the most tolerable thrill and provide other fun, more people will be able to have more fun.
A wooden roller coaster with an entire wooden structure came to mind. It was the first wooden roller coaster in Korea that no other theme park could imitate. All that was left was marketing persuasion.
● Old-fashioned? A feeling of deep satisfaction!
Manager Kim roughly divides roller coasters into four generations: first generation to fourth generation. First generation lifts the vehicle up using electricity or mechanical power and drops it. It changes potential energy into kinetic energy and repeats up and down. Second generation changes the material from wood to metal and changes the method of movement from up and down to 360-degree rotation or screw rotation. Third generation is innovation in the passenger seat. You hang, sit like riding a motorcycle, or ride standing. Fourth generation introduces a catapult method that launches aircraft from aircraft carriers like a slingshot, and launches the vehicle higher and faster. This is a change in propulsion method.
The wooden roller coaster is the first generation. Naturally, there were reactions like, “How much of a large investment is it to bring in something so old? And it’s dangerous.” “I rode it and it rattled so much that nails popped out.”
I persuaded them to lay the track with laminated wood, which is well-cut and processed wood that is compressed seven times at high temperature and pressure. The strength of the same area is similar to that of iron. They said they would use prefabricated wood instead of nailing it into the wood. They prefabricated it and assembled it by tightening it with bolts and nuts like Lego blocks. It is soft and less deformed, so there is less shaking or shock.
Driving comfort and safety alone were not enough.
“You could call it the law of diminishing thrill utility. The more you ride the most advanced roller coaster, the more your satisfaction decreases. Even if you bring in a 100-thrill ride, technology will rapidly develop, and soon 120- and 150-thrill rides will appear. So why would you come to Everland just to ride a 100-thrill ride? On the other hand, the first-generation roller coasters don’t give you much anticipation when you first ride them, and they stimulate the basic human fear of falling. The basic ones last longer.”
It emphasized the ‘best’ as the first wooden roller coaster in Korea, the longest operating length in Korea, the largest drop angle, and the fastest speed in Korea. After meticulous preparation, it was finally approved in August 2006. The installation site was the snow sledding hill. The sight of a huge wooden structure going up there in the mountainous terrain inside Everland was bound to be a big topic of conversation.
![The Law of Diminishing Utility of Roller Coasters – The Introduction of Korea’s First Wooden Roller Coaster[유레카 모멘트] The Law of Diminishing Utility of Roller Coasters – The Introduction of Korea’s First Wooden Roller Coaster[유레카 모멘트]](https://dimg.donga.com/wps/NEWS/IMAGE/2024/09/16/130049822.1.jpg)
● A series of difficulties
Park Myeong-gu, a construction engineer (then 37 years old, currently a freelancer), often resented the planning team leader who had been approved to install the wooden roller coaster as a sledding hill. The sledding hill site was so small that he had to place the space for numerous materials in a parking lot hundreds of meters away from the work site. The huge granite rock discovered during the excavation had to be dug up as is instead of being blasted away because of the customers. The foreign designer complained, “It’s too difficult to install it on your land.”
Originally, it was not the job to take full responsibility for the construction of the wooden roller coaster. When the ride was introduced, Manager Park’s technical department was in charge of creating the boarding area, restaurant, and shop. The main responsibility was the responsibility of the attraction technical team. However, they waved their hands, saying that the wood was not their domain.
I thought that the facility industry, such as theme parks, would be a bit adventurous, but when I took charge, everything from the drawing terms to everything was new to me. The 14-month construction period was a series of ordeals of overcoming obstacles I had never encountered before.
Based on a detailed topographic map measuring the terrain, altitude, and coordinates of the sledding hill, it was designed by a German expert designer named Stangl. The design of the pillars, ironwork, and other parts was done by the Swiss engineering company Intamin. The ironwork was done by Slovakia, the wood by Sweden, and the vehicle by Germany. The wood was treated with preservatives in Germany and it took 40 days to arrive in Korea via China by ship.
Building a foundation and erecting wooden pillars to build a truss structure according to a drawing has never been done before in Korea. When I went to the Korea Occupational Safety and Health Agency for a preliminary inspection with the drawing and safety plan, they said, “This is unprecedented, so we don’t know how to guide you.”
The problem was who to hire to do the work. I had no choice but to hire a carpenter and teach him. I went to Germany with two carpenters and learned how to build pillars. It seemed possible. The highest pillar I had to build was 33m, and I had to connect four pieces of wood. I installed two tower cranes. I connected the numbered pillars according to the drawings and went up like I was working on a utility pole, and assembled them with nuts and bolts. Carpenters did not like working at high altitudes. I hired people called ‘dobigong (工)’ at construction sites to work with me.
● ‘Mad Dog’
When Manager Park first saw the arrived lumber, he almost fainted. It had been warped after being exposed to the sun, rain, and wind for 40 days on the ship. When he contacted the company, they laughed and said, “That’s how it is. Assemble it yourself,” and introduced him to foreigners with experience. When they came to the site, they said, “There’s no preparation at all. You don’t have the right tools.” He ordered tools from an import tool store in Euljiro 3-ga, Seoul, and bought nearly 1 billion won worth of tools. He learned how to assemble the warped parts as they were through photos and videos.
The construction order was set in reverse order to match the test schedule a month before the official opening in March 2008. One day, the third ship carrying lumber had a collision while coming from China and was stranded. As a result, the ship carrying the necessary materials arrived first. They had to be assembled according to the column numbers according to the drawings, but they were out of order.
I wrapped my head around the absence data sent by the company and copied all of it into an Excel program and looked through it. Eureka! The numbers were different, but the length and thickness were the same. They were loaded on the ship that came later. They could have just pulled it out and used it. Since it was a mistake on the company’s part, they told me to make new parts and send them. The wood that was loaded on the third ship that arrived later was surplus material and was used to make fences and such.
It was a series of improvisations. Several of the pillars that had been connected to each other broke. If it was the top one, I could take it out, order a new one, and replace it. But taking out the bottom one would mean redoing half the project. After thinking it over, I added another piece of wood and tightened it, just like a splint when a person breaks a bone. Later, I checked and found out that it was the right way.
Once the opening date was set, he had to meet it even if he died. He persuaded workers who said they couldn’t work on Chuseok or New Year’s Day by saying, “Your children and grandchildren will ride it, so wouldn’t it be a proud thing?” and pushed ahead with the construction by giving them higher wages. During the construction period, Manager Park only rested for 7 days a year.
In December 2007, the American work team that came to lay the track returned, saying they would rest until Christmas and early New Year. Laying the track would support the entire structure and make it more stable. Manager Park said, “You saw what they did. Let’s do it,” and urged the workers to lay everything except the first section, which had a 77-degree slope. Later, the workers called Manager Park “Mad Dog.”
“If I hadn’t worked so hard, I wouldn’t have been able to finish the project on time and perfectly. It was something I couldn’t avoid, so I worried and studied a lot on my own. I had to take full responsibility for everything. I had no choice but to solve all the problems on my own.”
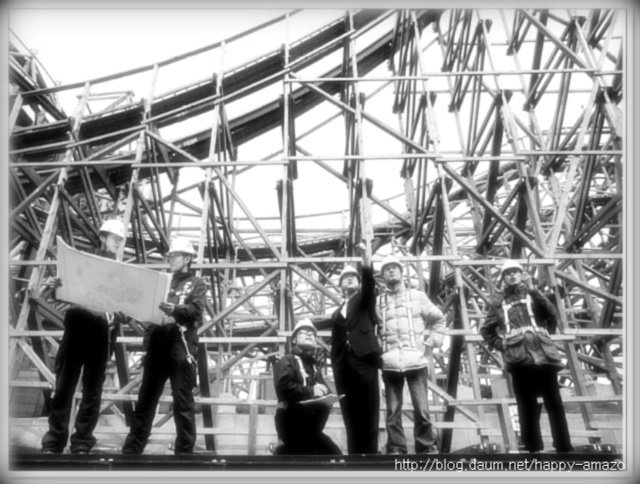
● Dummy, flying
In January 2008, it was the night of the first test drive. The American, Roden, who had 30 years of experience in consulting and supervising during the construction period, was in charge. Each seat in the vehicle was filled with a plastic bag shaped like a person, a dummy. As the vehicle was coming down from the first drop section, one of the dummies flew ‘boom’ against the moonlight. It was tied incorrectly. The hearts of those watching from below sank.
There was even an incident where a test vehicle got stuck in a ravine after the first drop and was unable to climb the next hill. It was determined that the track was not heated enough due to the cold and the train itself was not heavy enough.
During the test, shock sensors are installed on the vehicle to allow it to adapt to the shock to some extent. Afterwards, when it is deemed that a person can ride, a person gets on. Instead of removing dummies from all the seats, they are removed one by one. People sit down one by one starting from the removed seats. The first person to ride was Project Manager Kim Hwan-tae. He was the first person to ride the T Express, Korea’s first wooden roller coaster.
“My first impression after riding it was, ‘This is definitely possible.’ I’ve ridden a lot of wooden and iron objects around the world, but I’ve never had anything this fun. However, after riding it several times a day, over 100 times before the official opening, I eventually lost interest and started to worry, ‘Will the guests really like it?’”
In February of that year, a month before the official opening, a ‘soft opening’ was held. Wood needs stabilization. The wooden structure, which is assembled and installed with bolts and nuts, deforms slightly due to vibration during the test run. As it does, it finds its optimal position. The same goes for attachments such as sensors.
The soft opening is for employees, invited guests, and residents of the surrounding villages. It is also necessary to become familiar with the operation. Then one day, the vehicle stopped midway up. That day, the main TV news broadcast an article titled, ‘Everland amusement ride accident, hanging in the air for 15 minutes.’
In fact, it was the same situation as an AI self-driving car applying the brakes on its own to avoid an accident. It stopped because it was safe. At first, it was bad news, but later it had a noise marketing effect. There were no casualties, and a certain number of people learned that Everland had such a magnificent ride.
On the opening day, Manager Kim’s worries turned out to be unfounded. For safety and stability, only one of the three cars that can carry 36 people was in operation for a month. The waiting time was over four hours, but there was no end to people trying to get on. The moment the car entered the platform after about three minutes of operation, Manager Kim, who was waiting on the platform, saw passengers clapping. The passengers who got off the car and passed Manager Kim said, “Let’s ride this one more time.”
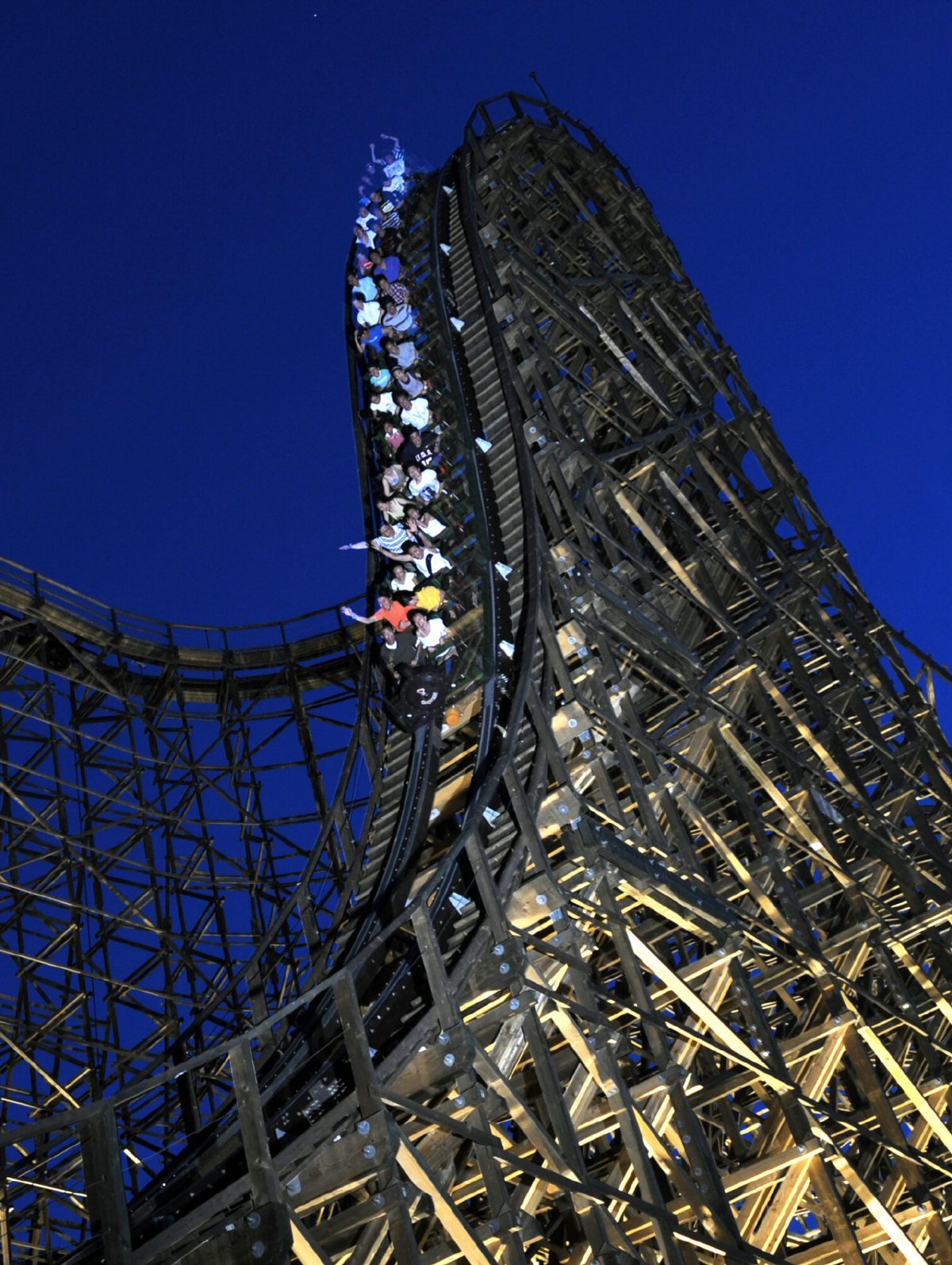
● Dreaming of another ‘wooden roller coaster’
Kim Sang-mu jokingly says that since the reconstruction of Gyeongbokgung Palace by Heungseon Daewongun in the 1860s, this was probably the construction project that used the most wood in Korea. The exact number of wood used is not known, but about 600,000 pieces of hardware, such as bolts and nuts, were used. While existing iron roller coasters use about 100 foundations, T Express used hundreds.
The budget was set at around 20 billion won in the master plan. When it was completed, it cost around 33 billion won. It is amazing that the company entrusted a large project with a budget of hundreds of billions of won to two managers in their early to mid-30s.
Kim Sang-mu said, “Should I say that the people in charge of planning trusted my words? I explained and persuaded them well with numbers and data on issues that were questionable. I think they accepted the will of the person in charge at the time.” Park, a former manager, said, “When I think about it now, it’s ridiculous. Should I call it the passion of youth or recklessness? I told the executives at the time, ‘I will set the standards here, so don’t ‘touch’ it.’”
Jeju Shinhwa World, Korea’s first and largest integrated resort where you can enjoy accommodation, dining, shopping, performances, entertainment, theme parks, and water parks all in one place, has never introduced a wooden roller coaster since T Express in a theme park in Korea. The reasons can be found in the fact that it is old, the thought that “there is one in Everland, so why bother with another one?”, and the lack of idle land where it can be installed.
Former Director Park said, “If we were to build another wooden roller coaster in our country, I would be confident that we could make it better by reducing costs, but we haven’t had the chance yet.” Perhaps the wooden roller coaster will remain as a dream and memory of the perfect ride for a long time.
2024-09-18 17:25:08