January 31, 2023
The active tags are loaded via wireless transmission and allow tracking the location and movement of all items in the store. The automatic line will go into full production in March 2023. Enables the production of IoT tags that include a dedicated chip and additional SMD components
In the photo above: Oren Bakramos (right) and Raviv Cohen from the Nexite company at the production line under construction. Photo: Techtime
Bekramos Technologies Company (Beckermus Technologies) of Caesarea established a new tag production line, in addition to Williot’s tag production line. The new line, which will begin serial work in the coming weeks, is intended to produce millions of smart NanoBT tags of the Nexite company (Nexite) Tel Aviv. The production line was established with an investment of more than 1.5 million dollars and is now in the final stages of installation, in a building purchased by Bakramos about two years ago with the aim of serving as a site for the customers’ dedicated production lines.
The Nexite company was established 4 years ago by CEO Anat Shaked and chief technologist Lior Shaked, and developed a hardware and software platform that enables the connection of physical products to the cloud for smart asset management and sales policy in stores and marketing chains. Today Nexite employs about 80 people, and since its establishment it has raised about 100 million dollars. During Techtime’s visit to the new production line at the site in Kerams, the director of hardware at Nexite, Raviv Cohen, said that the special tags provide accurate tracking of the product’s location on the shelves, which enables smart management of assets and stores based on information that can be extracted from them. Information that was not available until now in the hands of the managers.
A tag that is a local GPS
The technology is based on a combination of an active tag and local reception stations that know how to track its movement and identify its location in space. Cohen: “The detection is carried out by identifying the direction of the signal transmitted from the tag (Angle of Arrival) and triangulation of the signals arriving at several receivers on the site. It is a kind of local GPS. The local control station supplies the energy to the tag by transmitting signals at a frequency of 900 MHz. The internal circuit of the tag charges a capacitor and transmits Bluetooth signals at a frequency of 2.4GHz every 30 seconds.”
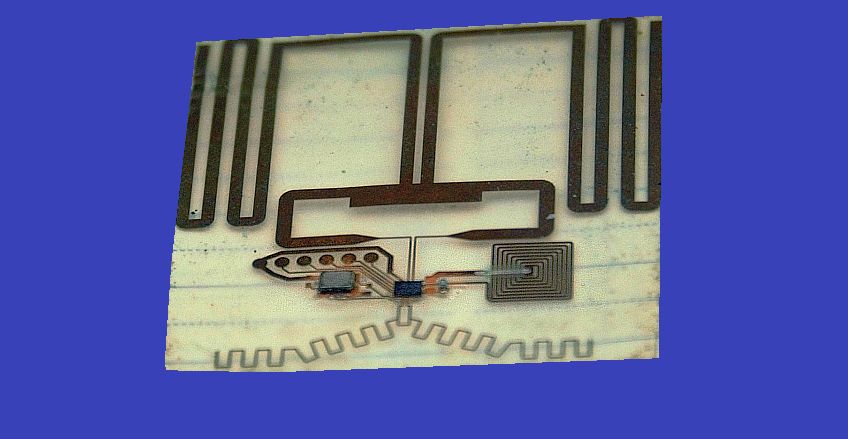
Each tag has a one-to-one identification number that is burned into the chip in an earlier testing process. This allows the company’s systems to collect data on the tags, identify the customer’s reference to the product on which the tag is found, and also which products sell better than others. Based on this information, Nexite provides insights designed to increase sales. The Nexite company is preparing for the start of sales in 2023, and in the meantime it is carrying out large-scale pilot projects with large brand chains in Israel and abroad.
Breaking the standard production limits
Cohen: “In our business model, the cost of the tag is a critical element. We are in a mass market on a scale of hundreds of millions of items. The cooperation with Bakrams allows us to develop the production line suitable for these limitations, and to guarantee a production solution for the coming years. About two years ago, we approached Bakramus and raised the need for the establishment of an Israeli production line, which part of the time will also be devoted to development and not only to serial production.”
A joint manager at the Bakrams company, Oded Bakrams, said that in the first phase the new line will produce the tags at a capacity of 5,000-6,000 tags per hour. “NanoBT tags include three different components, including a chip developed at Banksite and manufactured at TSMC. The suppliers we contacted abroad expressed concerns regarding the complexity of production. We entered a learning process and developed a customized line, based on systems we purchased about a year and a half ago. The machines arrived in Israel just a few days ago and the line is currently being installed.”
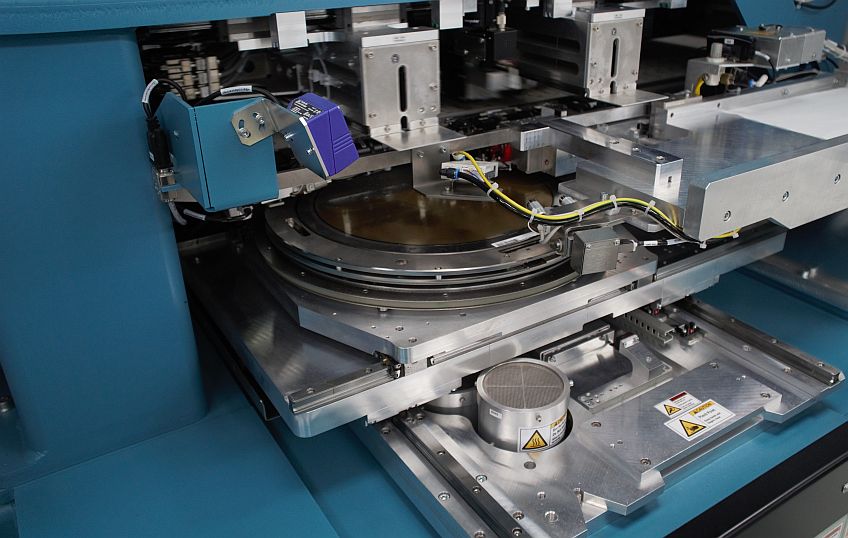
Oren Bakramos (joint director) said that the production line that was sewn for Nexite needs is built in a Reel to Reel – R2R configuration and includes 6 different machines with a total length of about 15 meters. This is an unusual and fully automatic production process: production begins with a flexible plastic roll on which the special antennas are printed. This roll is fed into a machine that contains the dedicated chips in the configuration of a sawn silicon slice.
The machine picks up each chip (a sawed-off piece of silicon) from the wafer, according to the wafer production efficiency profile received from the chip manufacturer, and sticks it to the tag’s antenna. Later, the tag goes through an SMT machine that mounts the additional SMD components on it, and the assembly process ends at a functional test station that tests each tag individually in order to map the tags’ performance. In the last step, another plastic layer is glued on the tag which protects it. The system is planned to enter serial production as early as March 2023.
How did you manage to set up such a challenging production line?
Oren: “We are a company that has been assembling chips since its inception, and this is our specialty. We know how to deal with wipers, pack chips and integrate them into the final product using a variety of technologies. We used this machine to adapt the Muehlbauer production line to the Nexite project. Basically, production lines for RFID are simple, but we were required to integrate three additional components into the tags, and this is a challenge that has not been carried out to date.”
In addition, Karams and Nexite have developed a production process based on the use of electrically conductive glue instead of soldering. This glue contains nickel nanoparticles that provide an electrical conduction property only at the point of pressure – a phenomenon that eliminates the need to use masks as is done in the soldering process. However, it is very important to place the components on the surface with micron precision, in order to achieve electrical conduction.
Oren: “The collaboration with Nexite began after we identified the IoT as a rapidly developing breakthrough field, and we decided to invest in it. Since it is a fully automatic production process, this line also has the special added value of competitive Israeli mass production capability – independent of manpower costs.”
Posted in the categories: IOT, news, manufacturing and subcontracting, Israeli industry
Posted in tags: Beckermus, IOT, Beckermus, electronic manufacturing