2024-08-03 06:29:26
Celltrio Launches First Automatic Cell Line Cultivation System
Korean-American robotics experts join hands to commercialize cell line automated culture system
Difficult manual work done by humans… Robotic arms carry out the entire process without mistakes
Focus on 2-4 Billion Won System… Likely to Contribute to Acceleration of Biopharmaceutical Development
Cell culture is a process that must be done without fail in a laboratory developing biotherapeutics. The cell line that is the subject of the research must be cultured to increase the number of individuals to enable various experiments. Researchers wearing white coats handle the cells with delicate hand movements in a sterile environment, and increase the number of cells by supplying culture fluid while being careful not to contaminate them. They must also check with a microscope to see if the cells are growing healthily. In order to store and extract the necessary cells, they must also frequently handle an ultra-low temperature freezer maintained at minus 150 degrees Celsius.
Celltrio (CEO Charlie Duncheon), located in Fremont, California, USA, is the first startup in the world to commercialize a fully automated cell line culture system. Its customers include the National Institutes of Health (NIH) and leading global pharmaceutical companies.
The person who proposed to CEO Duncheon (73) and co-founded the company is Chairman Kim Jin-oh (65) of Robot & Design. Chairman Kim, a robotics expert, is the Chief Technology Officer (CTO) and largest shareholder of Celltrio. He is still continuously developing automation system technology using robotics. He learned about Celltrio while looking for a startup targeting the global market. I met him at the Korea Robot Industry Association in Yongsan-gu, Seoul on the 30th of last month. He was elected as the Chairman of the Robot Industry Association this year. Appearing with a black backpack, he said, “I have spent my entire life in robotics and the research results I have accumulated while developing an automation system for bio lab equipment for the past 15 years are now beginning to see the light of day.”
● Available for cultivation 24 hours a day, 365 days a year
![Robots are ‘quickly’ carrying out 24-hour automatic cultivation… “Global pharmaceutical companies are placing orders one after another”[허진석의 톡톡 스타트업] Robots are ‘quickly’ carrying out 24-hour automatic cultivation… “Global pharmaceutical companies are placing orders one after another”[허진석의 톡톡 스타트업]](https://dimg.donga.com/wps/NEWS/IMAGE/2024/08/02/126289732.9.jpeg)
A laboratory for culturing cells is not just for cell culture, but it usually takes up 99-132㎥ (about 30-40 pyeong). Celltrio’s automatic cell culture system (Robocell) is slightly different in size depending on its function, but it is usually about 4m wide, 3m long, and 2.8m high. If we compare only the area, it only needs 12㎡ (about 3.6 pyeong), which is about 10% of the laboratory area. It can operate 24 hours a day, culturing cells 365 days a year without human intervention. Another advantage is that all processes related to cell culture are recorded in software, making it easier to consistently reproduce experiments or research more efficient culture methods.
The Robocell is made up of multiple independent modules (components) that include an ultra-low temperature freezer to store cell lines, a liquid handler to divide cells into multiple containers, a medium supply to deliver nutrients to cells, and a centrifuge and cell counter. “It is possible to initially use only a few functions and then switch to a multi-functional large Robocell as needed, and it is also conveniently compatible with external solutions previously used in laboratories,” said Chairman Kim.
The Robocell moves flasks and well plates (plates made to hold many containers at once) around using a transport device and robotic arms in an internal sterile space. Chairman Kim said, “We are the first to have a robotics system that automates the entire cell culture process like the Robocell,” and “Thermo Fisher Scientific, a global biotechnology company in the U.S., is selling the Robocell in Europe as our agent.”
Another automated device from Celltrio is the Robostor, a cell ultra-low temperature freezer. It is a device that stores cells by lowering the temperature to minus 150 degrees Celsius. It automates the process of manually removing sterile vials containing cells from the freezer. It removes the vial containing the desired cells without error from among tens of thousands to thousands of vials. When the freezer is opened, a person may accidentally take out the wrong vial due to the cloudy vapor that is generated, which can cause their vision to be blurred. Also, when a vial is taken out of the freezer, the glass vial tends to freeze due to moisture in the air, but Celltrio solved this problem by creating a temporary space that pushes out all the moisture in the air. Chairman Kim said, “The ultra-low temperature freezer is connected to the Robostor, but it is also supplied as an independent product because there is so much demand.”
● “Continuous orders from global pharmaceutical companies”
The automated cultivation system was first installed and approved for use by a global pharmaceutical company this year. Chairman Kim said, “It’s been about two years since we received the order, but since the final finishing touches were completed and the global pharmaceutical company finally approved the product, we can say that full-scale sales began early this year.”
Celltrio posted sales of $700,000 (approximately 950 million won) last year and expects to post sales of more than $22 million (approximately 30.074 billion won) this year. As news of the development of the automated culture system spread throughout the industry, global pharmaceutical companies have been pouring in orders, and the company has received more orders than its target for this year. Chairman Kim said, “Depending on the scale of the installation, (the system) is usually sold for 2 to 4 billion won, and there are customers who plan to order five units at once.” NIH and Thermo Fisher Scientific, which has annual sales of $42.8 billion (approximately 58 trillion won), are also customers. Celltrio’s recent $3 million investment is to expand its production and service capabilities in response to the increased order volume.
Robocell currently manufactures hardware at Robot & Design, and Celltrio in the US supplies the software Bioflow that operates Robocell, after optimizing it to customer demand. Robot & Design, a company specializing in robots and automation equipment established in 1999, develops hundreds of types of robot equipment and sells them in the form of original design manufacturing (ODM) or original equipment manufacturing (OEM). Chairman Kim said, “We are also pursuing a plan to produce directly in the US in preparation for increased production.”
● Top Korean and American robotics experts join forces
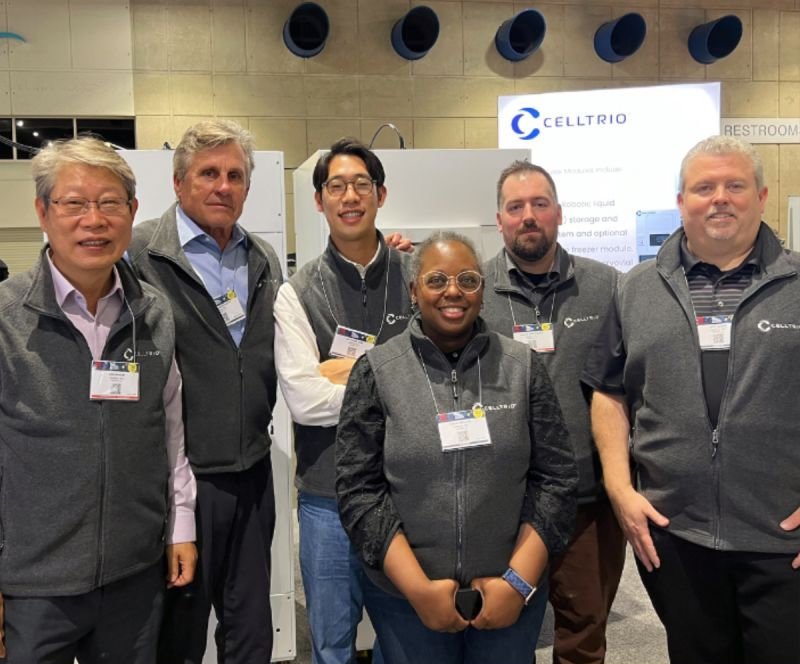
Chairman Kim and CEO Duncheon are robotics experts from Korea and the United States. Both have been using robotics to create industrial automation devices for over 30 years. Both have received the Joseph Engelberger Leadership Award, the highest honor in the U.S. robotics industry.
Chairman Kim received his bachelor’s and master’s degrees in mechanical engineering from Seoul National University, and was the first student to enter the world’s first doctoral program in robotics at Carnegie Mellon University in the United States, where he received his doctorate in 1992. From 1994, he worked as the first head of the robot business division and the first head of the robot development group (department head) at Samsung Electronics for 4 years and 9 months. From 1999 to 2021, he was a professor in the Department of Robotics at Kwangwoon University. From 2001 to 2008, he contributed to establishing the government’s robot-related policies and strategies. Through Robot & Design, etc., he has developed over 400 robots and automation systems in the semiconductor, bio, and medical industries to date.
Mr. Duncan received his bachelor’s degree in industrial engineering from Purdue University and his master’s degree in business administration from Southern Illinois University. He joined Adept Technologies, a company specializing in industrial automation and robotics, in its early days and served as its chief commercial officer, where he played a role in achieving $100 million in annual sales and a successful initial public offering (IPO).
Celltrio is currently focusing on research and development, and plans to develop the developed cell culture automation system so that it can be used in the production process. It also plans to add intelligence to the system so that more efficient cultivation can be achieved through data collected during the cell culture process.
Chairman Kim said, “Celltrio will become a company that serves as a cornerstone for overcoming human diseases by helping with innovations such as basic research and development of new drugs and mass production of biopharmaceuticals.”
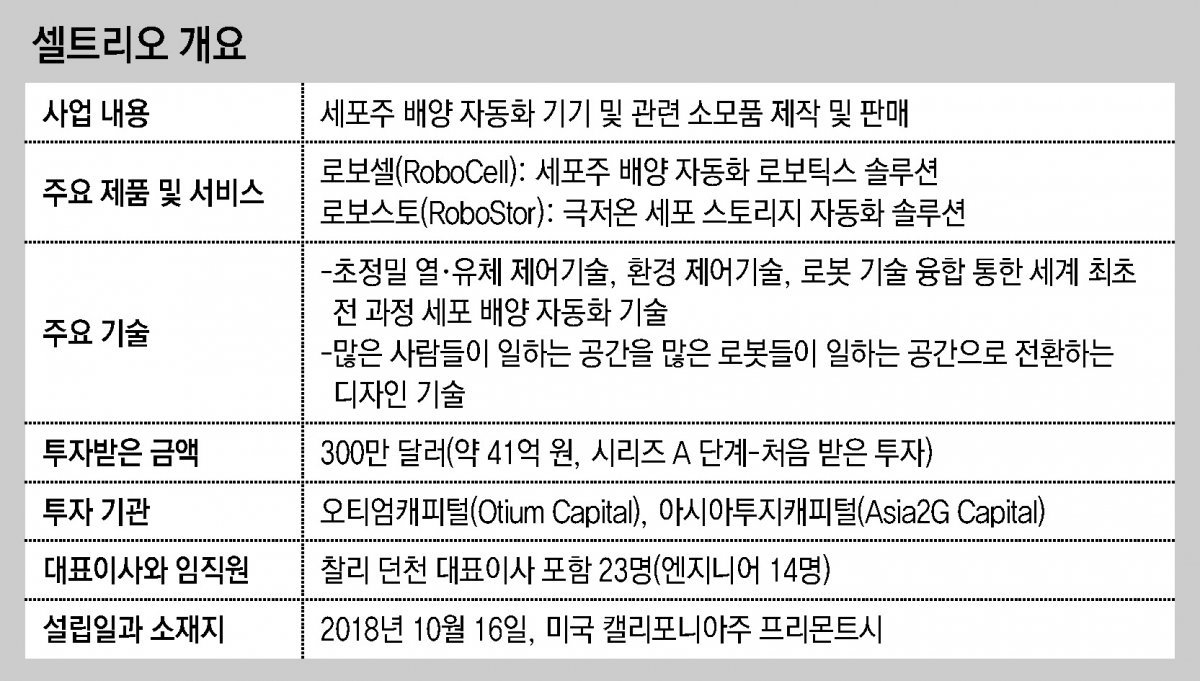
Reporter Heo Jin-seok [email protected]
2024-08-03 06:29:26